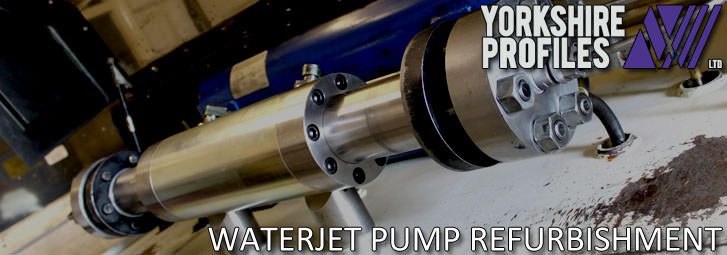
Over time waterjet pumps lose performance and efficiency reducing the speed at which they can cut in order to maintain a high quality cut finish. This means it is necessary to strip the pump down and to fully check all the chambers for scoring marks, the ceramic plungers for damage and pretty much every other component for any hairline cracks or damage.
Great care has to be taken when working on a waterjet pump
Waterjet pumps are quite simple in principle. A chamber fills with water from a mains supply and a ceramic plunger is then pushed into the chamber creating the 55,000 psi of pressure. This is achieved with a very powerful hydraulic motor and a sensor which lets the system know the location of the plunger.
The waterjet pump is quite simple in it’s design (various seals and valves not labelled)
The high pressure water enters an attenuator before reaching the nozzle on the machine. This attenuator prevents any fluctuations in the cut quality created by a pulsing of the water pressure inline with the stroking of the pump.
The assembly is carefully stripped down and refurbished checking for any hairline cracks.
Any components which have scoring marks or cracks have to be completely replaced immediately as the pressure of the water in which they store will soon cause catastrophic damage.
The high pressure water cylinder pressurises the water to 55,000 psi using a ceramic plunger.
Even though all the components are of a high specification, pollutants which may enter the system over a period of time (including seals which have broken and disintegrated) create internal scratches which reduce the plungers ability to generate a constant pressure, or they can create “heat spots” which reduce the life of high pressure seals further increasing debris inside the pump.
The waterjet pump is carefully put back together.
The waterjet pump is fully refurbished and ready to go.
Whilst the pump is being refurbished, it is a good time to clean the actual waterjet cutting machine as this can also take approximately 2 days.
The waterjet tank fills up with mud (abrasive sand and steel particles) over a long period of time. Even with the mud pump, it still needs manually digging out.
Usually this task is reserved for bank holidays or during the Christmas shutdown period, however whilst the pump is out of action it makes sense to get it done now.
Inside the empty waterjet tank you can see the mud pump grates which help keep the tank empty.
Waterjets are not the nicest looking machines, but they are very durable.
Even after all of this we were faced with a challenge. The hydraulic motor decided to fail at the end of the refurbishment which meant that the pump was simply unable to generate pressure. This meant that the waterjet cutting machine was out of action for a whole week whilst we had the motor refurbished too. After which, we now have a fully refurbished pump generating a constant high pressure for high quality cutting.
The hydraulic motor on our waterjet pump.