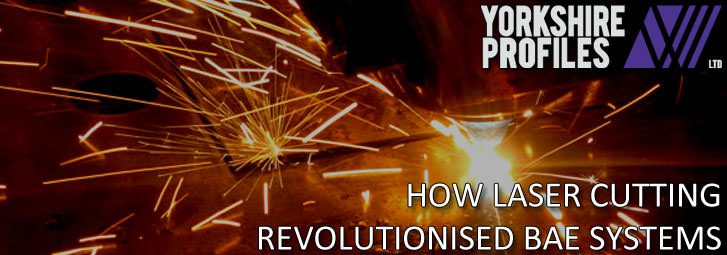
Laser cutting is a service which is used in more walks of life than most people realise. Its versatility and precision is matched by nothing else, which is why so many industries are choosing to embrace it. One of the companies that laser cutting has completely revolutionised is BAE Systems.
BAE Systems are a British multinational defence, aerospace and security company that have operations all over the world. They are one of the most important companies today, as they have an impact on how we progress with different technologies.
Yorkshire Profiles are always interested in how laser cutting has changed different industries, which is why this blog will showcase the different ways laser cutting has allowed BAE Systems to grow.
New Broad Oak Microwave and Microelectronic Capability
A trusted partner of BAE Systems is Maritime Services, who provide manufacturing and various life support services that have integrated electronic systems, subsystems and modules for different applications.
One of the main services they provide is through the use of microwave technology. These devices are able to perform a number of different and normally difficult processes, as one of their main features is laser cutting.
These machines utilise a CO2 laser to cut a variety of different materials to a high level of accuracy. Although these types of lasers aren’t optimised for thicker materials, when it comes to straight line cutting and piercing, it’s tough to find another machine than can match the same speed.
This type of laser cutting machine is a popular choice for a lot of businesses due to the finish it provides. The surface will always be smooth, making the piece of material safer to handle. Using CO2 laser cutting can prove to be a versatile advantage as it is able to work with wood and acrylics, materials that other laser cutting systems can struggle with.
The machines used by Maritime Services are also able to use YAG laser manufacturing for cutting, marking and welding. YAG technology, short for neodymium-doped yttrium aluminium garnet, uses a crystal to produce a laser. It’s precise enough to engrave, etch and mark on both plastics and metals.
For BAE Systems, this laser is used for welding purposes. Being able to seal tough materials such as aluminium and kovar is essential when creating different forms of transportation.
With Maritime Services having two different laser cutting systems that BAE Systems can use, it’s little wonder they work in so many sectors.
The Introduction Of Amada Laser Cutting Technology
As of 2012, BAE systems installed a new FO3015 MkII 4kW laser cutter at Her Majesty’s Naval Base in Portsmouth. What makes this machine unique is how it has an attached rotary index tube cutter to help with the processing of ship components.
Previous manufacturing technologies were only basic and required a number of hours to be invested. There was also a high level of room for error which could push back ongoing projects significantly. Once this laser cutting technology was installed, BAE Systems noticed an instant increase in efficiency.
This is important for HMNB Portsmouth, as it’s the home port for over 60% of the Royal Navy’s ships. Although the base was first established in 1194, current core operations include repairs and shipbuilding. Well over 3,000 BAE Systems employees work at the base on a daily basis, regularly producing sizeable items.
Although the base has existing laser cutting devices, they aren’t optimised for working with light materials, which can be anything between 1mm and 20mm. They decided on the FO3015 because it also offers tube/section cutting as well as an excellent plate and flat sheet processing. This allows BAE systems to avoid having to rely on sawing machines.
With over 45,000 components that can be laser cut with this machine, it’s a worthwhile machine to have. It’s able to run all day, allowing everybody at the base to cope with the highest of demands. A number of manufacturing processes may need to be completed throughout the day, which it can easily do.
When it comes to materials the FO3015 doesn’t struggle. It’s able to process standard metals such as steel, aluminium and stainless steel, as well as unconventional materials such as, plywood, certain rubbers and armour plate.
It’s allowed BAE Systems to ensure Her Majesty’s Naval Base is more environmentally friendly. The previous laser cutting devices were producing a number of waste off cuts which weren’t able to be re-used. These devices meant that they needed to purchase specially sized materials, something which was costing a lot of money.
Thanks to the Amada laser cutter, BAE Systems now have a better control over their inventory, and there’s no need for extra processing thanks to the final cut producing a clean finish.
Model UAV Model For BAE Systems
On the 18th of July 2014 the Farnborough Air Show took place. The event played host to a range of different aircraft types in flying and static displays for the public. An interesting aspect of this show is the future section, where companies from all over the world showcase concept aircraft models.
BAE Systems wanted to show of a concept UAV (Unmanned Aerial Vehicle) that’s part of their FVAS (Future Combat Air System). There was little time to get this model, meaning they weren’t able to carve a master model to take a mould from. It was essential that the model was lightweight, but that created the problem of not being able to use a solid material.
They chose to create a 3D CAD (Computer Aided Design) model with only basic referencing material. The specific design requires ribs that intersect at certain points to keep the model together. Laser cutting allowed this to happen, providing them with an outer skeleton that only required a single piece of birch plywood.
To create rigidity as well as a smooth surface, a thin layer of fibreglass was then added to the model. Once this was done, a coat of high build primer was added before being sanded down to leave a smooth surface. Finally, a coat of grey paint was added to give it a realistic look.
Although all this may sound like a traditional way to create a model, very rarely is laser cutting with CAD software used. It may only be a simple process, but BAE Systems have shown how these processes can be used to help tasks, like model making, easier to create.
Thanks to laser cutting, they were able to design the model with a purpose built holder for a tripod stand for it to be hung from the ceiling.
Laser Cut Steel For New Patrol Ships
One of the more recent uses of laser cutting for BAE Systems is steel cutting for the first of three patrol vessels. This was done in October of this year (2014), at BAE Systems’ own shipyard. The contract is worth just short of £348 million, and has saved over 800 jobs.
When it comes to the measurements of these vessels they have to be incredibly specific. The average ship weighs around 3,000 tonnes, including all the equipment and engine components, and it has to be able to float in water.
Each of the Royal Navy Offshore Patrol Vessels will be 90.5 metres in length and 12 metres in width. They will be complete with a single 30mm cannon as well as an enhanced flight deck. It’s a new form of ship that will change how vessels are designed in the future.
Without the use of laser cutting it’d be impossible to create the unique shape of these ships. Thanks to the use of CAD, it’s easy to cut the steel to make these vessels a reality. The MOD (Ministry Of Defence), Chief of Defence Material Bernard Gray, started the laser cutting process himself at an official ceremony.
It will be exciting to see what the final result will look like. Due to the reliability of laser cutting, we’re betting that it stays very similar to the initial designs.
BAE Systems, Laser Cutting and What It Means For The Future
These may only be four different ways laser cutting has changed how BAE Systems work, but there will be many more that are done behind the scenes that are yet to be announced. However, there has been a significant impact, and it’s amazing how many new jobs this diverse process can do.
If BAE Systems have openly embraced this technology and are proud to share it with members of the public, it won’t be long before it’s used in even more industries. There are a number of ways laser cutting can make a person’s job easier, it’s just up to them whether they embrace it or not.
What do you think of this blog? Do you know of any other industries that have already embraced laser cutting technology? Let us know in the comment section below, or contact us on Twitter: @YorksProfiles.