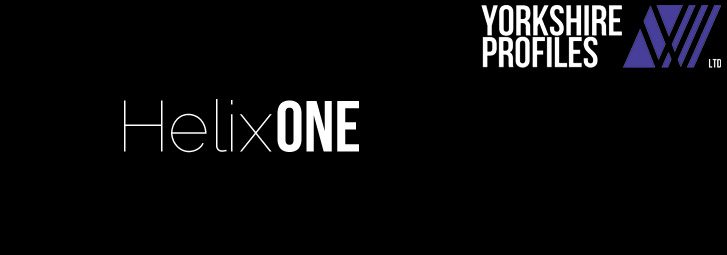
“Employees are a company’s greatest asset”… is a saying which I tend to disagree with, but hear me out. I don’t like the saying because it dehumanises the team, it puts people on a comparative scale vs equipment and a bank balance. But I won’t stand on a soap box on this one just yet.
Other than to say, we are going to be looking at our management of “Assets” in part two, and this almost exclusively applies to physical assets. For this, we have created HelixEAM (Enterprise Asset Management). I have avoided some screenshots of our system, as the layout and data on some pages is key to our efficiency over competing products. In this post, we will show how we maintain live records and how we greatly improved accurate completion of maintenance records with enforcement.
As a small business, it’s easy to overlook the importance of maintaining accurate asset records, and often even those of strong will slip under pressure, but the benefits have huge financial implications on the bottom line.
Tracking major purchases tends to be pretty easy, as there is a lot of paper work and finance agreements to monitor. But what about that occasional angle grinder that breaks and one of your team nips to the local DIY shop to grab another? Do you know how much you paid for it? Did you get your moneys worth out of that brand? Was it maintained properly to maximise its life? It might not seem like much, but when you have unnecessary purchases or repairs of grinders, sanders, polishers, measuring equipment and all the other bits and pieces that make up your workshop, it soon erodes your profits. Not to mention time lost!
Our old EAM used to work really well, and still does up until a certain level of production pressure appears. The cause of its failure, was that it was partially paper based.
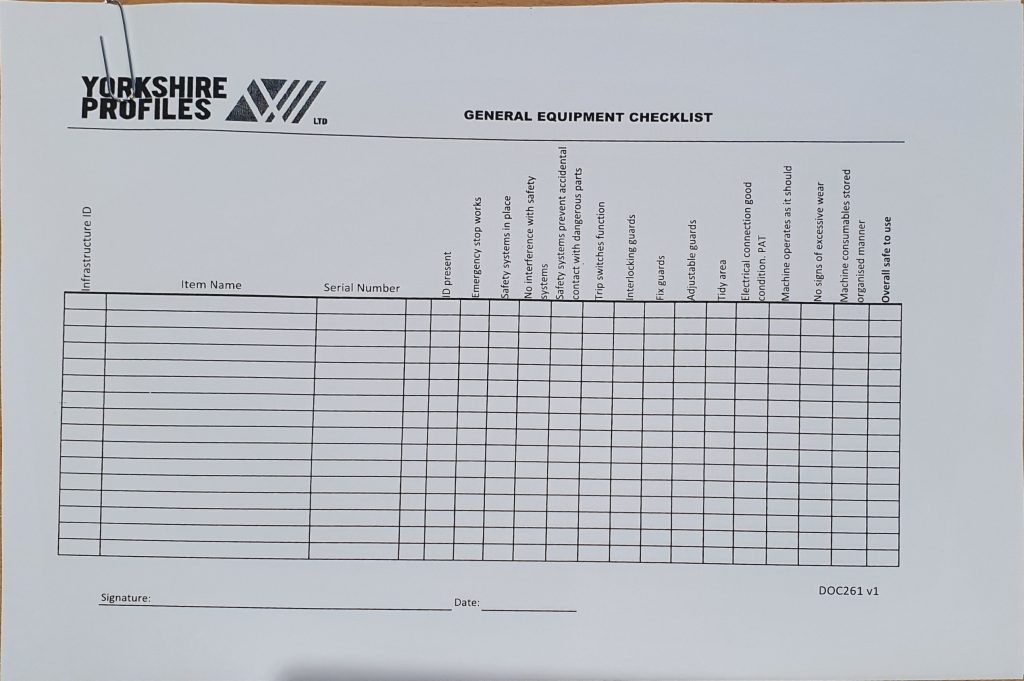
We’ve found there is a crucial balance of Convenience Vs Enforcement when it comes to designing a new system.
Problem Number 1: I’ll register it later
First scenario, an assumed old angle grinder has broken down. You’ve checked what you can (fuses, carbon bushes) but it just isn’t working. You think it’s done pretty well to last as long as it did so you send someone out to grab another one. When they get back the clock is ticking on this order, there isn’t time to get this registered on a system, just start using it and it’ll get logged later…. time goes by and the purchase gets buried in accounts. Oh dear, another anonymous grinder in the workshop. You also fail to spot the grinder wasn’t that old, and the reason it failed? The ventilation holes had become blocked. *Sigh* again.
The first step is to make it as easy as possible for new equipment entering the workshop, and old equipment leaving the workshop to be registered. I mean, really easy. We achieve this by having it possible within 2 clicks of logging into the system, whether on a desktop PC or a company tablet located in the workshop itself (no excuses!). All of our assets can fit into pre-determined categories:
- Ancillary
- Fixed Plant
- Handheld Tools
- Health And Safety
- IT Equipment
- Measuring Equipment
- Portable Equipment
- Storage
- Transport
The user just needs to click on a category and add an item. The important thing is that a name for the item exists on the system, other details can be saved/updated later.
Our users then have two options, they can either put a company printed sticker on the item (which contains a QR code for the items identification (encrypted to prevent address bar manipulation)) or they can attach a RFID tag. QR codes are the preferred method, mainly because its pretty much free to apply. However, in the case of handheld tools, or outdoor items, these can become damaged and unreadable. In this case, we apply RFID tags to identify the item. Simply scan the tag and attach.
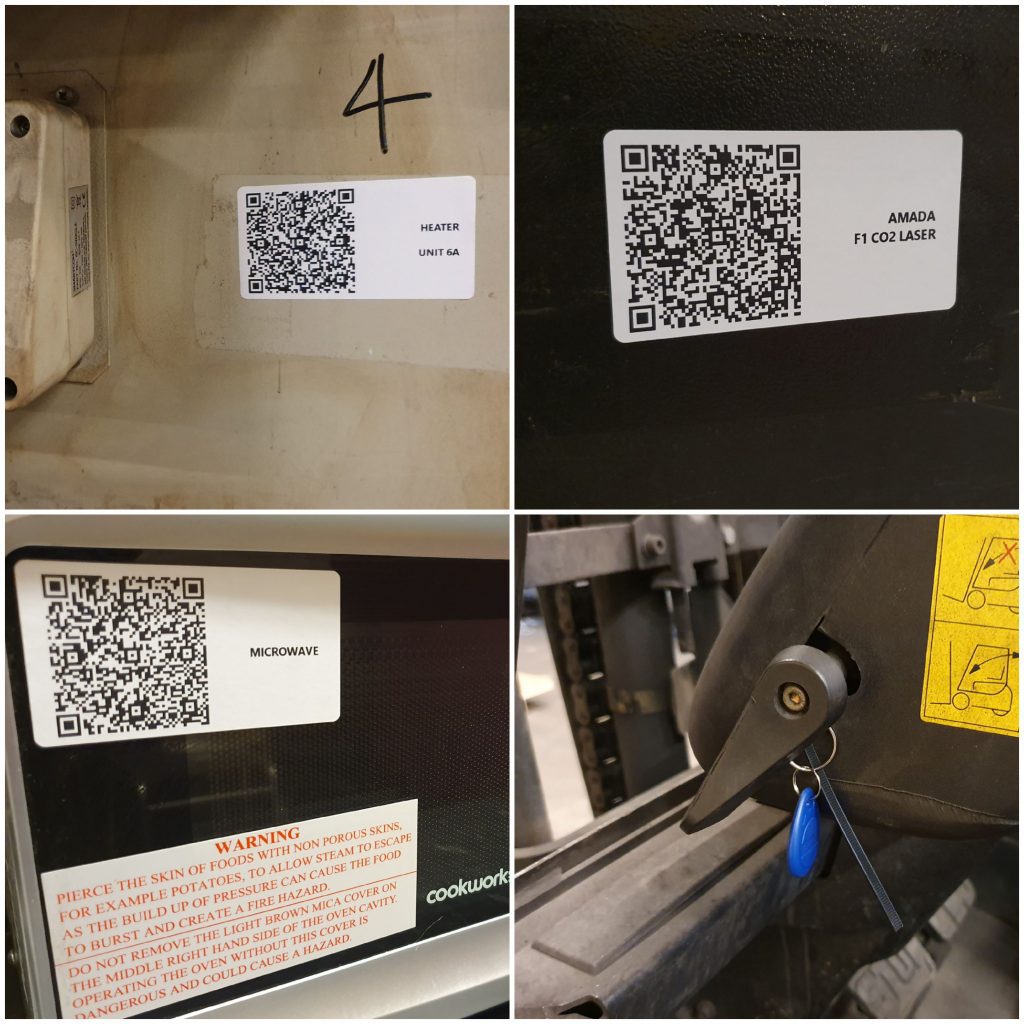
FUN FACT: “Address bar manipulation” is where someone uses the address bar in a web browser to manipulate data on a website or database. By encrypting posted data even on internal requests, we can prevent anyone from trying to beat the system and complete records which have not been completed.
Key data includes the purchase date and purchase cost of the item. From this, we can follow live value depreciation of the item as it ages. If we have records of maintenance and the item fails before it has fully depreciated in value, we might want to try a different brand or a more heavy duty tool. Going out to buy the same replacement tool would be a mistake. In an ideal world, all assets should be fully depreciated before disposal (unless you are selling it on).
Problem Number 2: It was checked, but not checked.
The problem with paper based records and even many digital systems, is the lack of enforcement. I’ve seen it many times where the workshop is rammed with orders, and the priority quickly becomes to just get the work done. Disaster. As maintenance and regular checks get put to one side during busy periods, things become less efficient quickly (not to mention unsafe!). Thereby increasing the time taken to complete work, only in small percentages to begin with, but this builds. A quick checkup on a machine operator for his maintenance check sheets and they’ll sometimes have the nerve to quickly tick all the boxes in front of you and sign it off…. for the week. They insist they did the checks, just didn’t have time to complete the document, or couldn’t find a pen.
Introducing daily rounds to check to see if the checks have been done daily can become cumbersome and time consuming, especially over multiple buildings or when you only have a small team. We need to be able to see who hasn’t done their checks and automatically eliminate those who have. Not only that, but we need to be certain they have done the checks and on time.
For this, we introduced a level of enforcement. Digital check sheets can quickly be created in our HelixEAM. Every check sheet automatically starts with question one “Can you identify the item?”, the system will then ask for proof. Check sheets are created for equipment type sub-categories (eg. Air Compressors) so 1 check sheet can be created and applied to multiple pieces of equipment of the same type, easily.
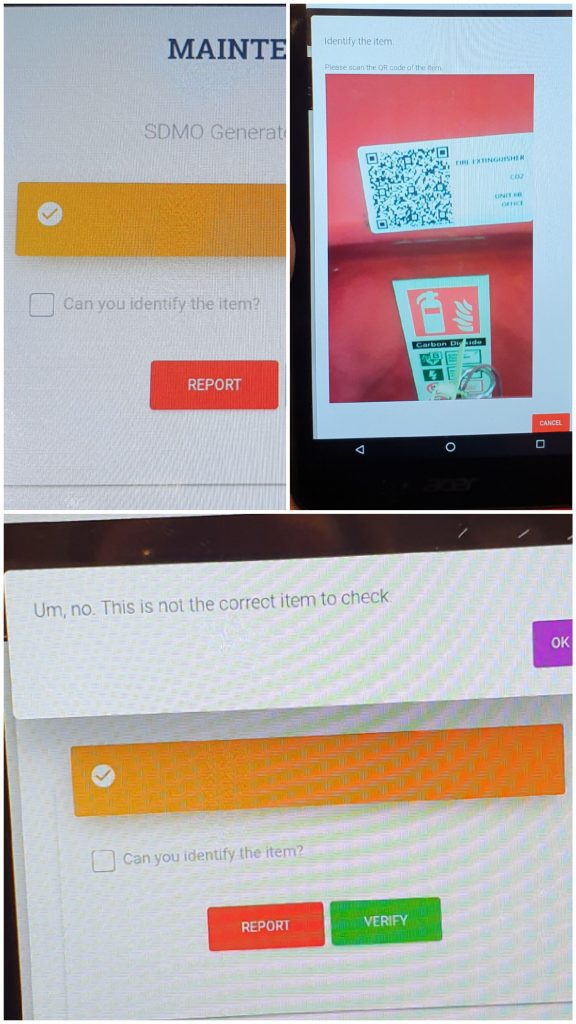
By actively requiring the user to be at the correct location on certain equipment before they can proceed, it greatly increases the accurate completion of records (and yes, it’s timestamped live against when it should have been done). It was quite easy writing a QR code scanner directly into our application so again we are not having to use third party software.
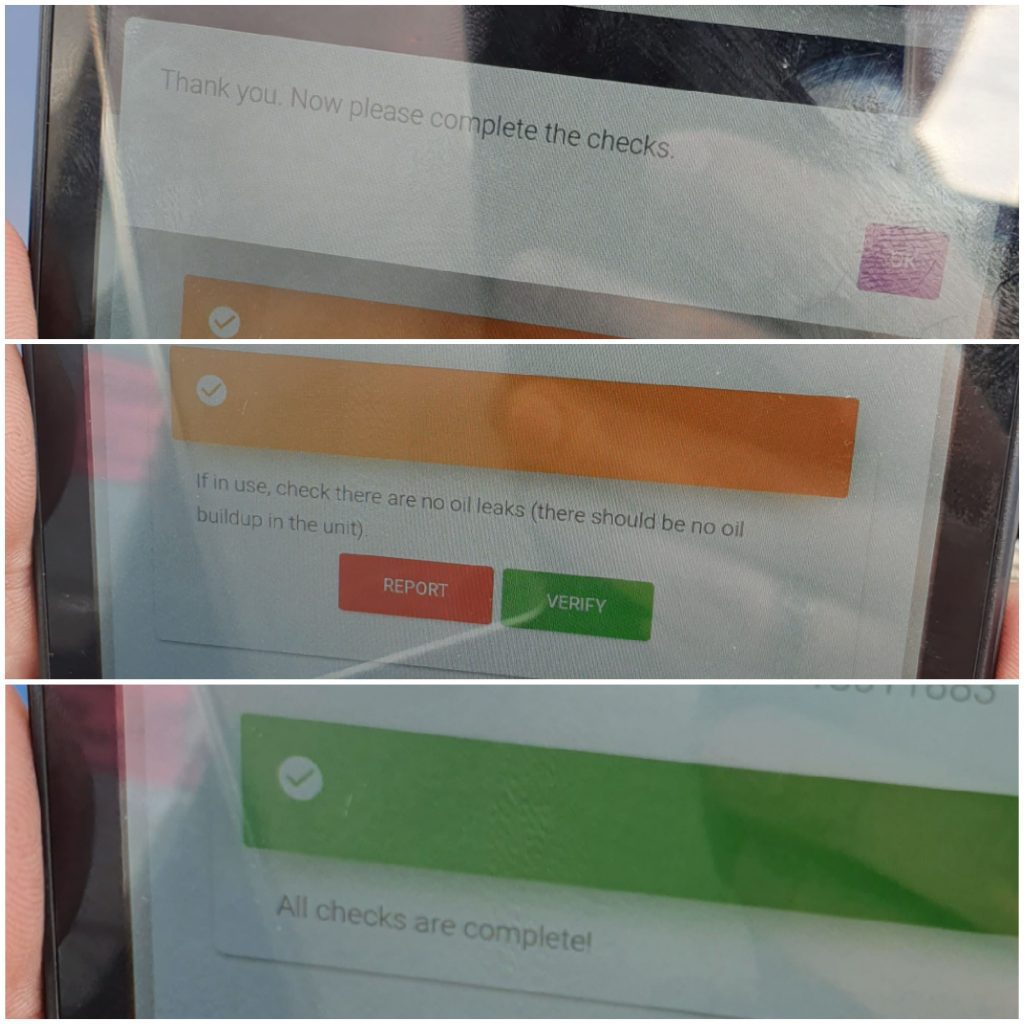
Every user can only see their own checks as not to cause confusion or duplicates. The Directors have master control of the system and as it is cloud based it can be used anywhere in the world. For example, lets say Person A is under a lot of pressure with their workload, but Person B is competent to carry out the checks which are flagging on my quality dashboard as due. With 1 click I can simply move the checks over and they will then appear on Person Bs tablet for immediate completion.
Or even, the Quality Director is out of the office for the day, but they can see on their tablet that the daily quality check for the forklift has not been completed by 9.am. Someone will be getting an angry phone call back at the unit. It will only happen a couple of times before this is not an issue any more.
As one additional benefit to this system, users can use their tablets to scan the QR code or RFID tag on any equipment to report an issue. They do not need to find a manager, or insist they told someone weeks ago. All data is live throughout the whole system, simply scan and report and it will appear on a Directors screen (or phone, or tablet) for immediate investigation and resolution. Better still, the Director or Manager can quickly log an action plan with assigned users and timescales and this feeds back immediately to the tablet.
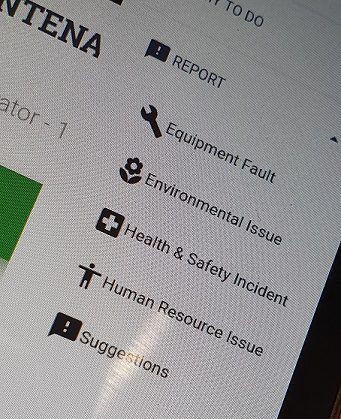
“This is my tablet. There are many like it, but this one is mine. My tablet is my best friend. It is my life. I must master it as I master my life. My tablet, without me, is useless. Without my tablet, I am useless….”
We anticipate this new method will greatly improve the quality of care our assets receive. Minimising downtime, preventing costly breakdowns and generally improving the high level of safe workplace we are seeking. What are you thoughts? Have you experienced similar issues in your workplace? @YorksProfiles