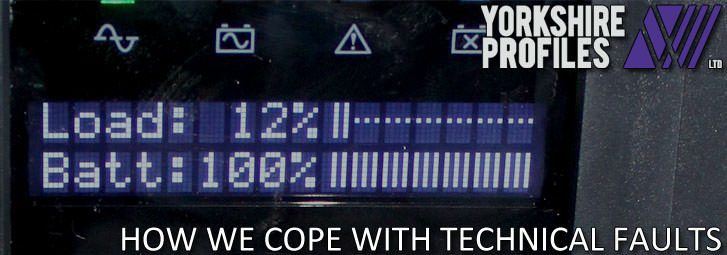
Even the most efficient businesses run into technical problems and the occasional bad luck. That’s why it’s important to know that your metalwork supplier takes these threats seriously and has contingency plans in place, more than just the financial insurances to protect their interests but action plans that will help protect you as a client from disruption.
At Yorkshire Profiles all of the metalworking equipment we use is subject to frequent inspections, testing, calibration and servicing by the manufacturer of the equipment. We also have service contracts on the major production equipment to ensure that in the event of a problem we are a priority case and can have an engineer on-site within 24 hours to correct the issue.
One of our claims as to why you should choose us as your laser cutting supplier is because of our integrity and honesty and we believe we have recently demonstrated that to all of our existing clients. Recently our laser cutter was hit by two faults simultaneously and our action plans were put into action. We had an engineer on-site very quickly who diagnosed the issue with our cooling unit and ordered the replacement parts as required. Our order books and production schedules were analysed and all clients who might have become affected by potential delays were contacted and informed of the issues we faced.
By the end of the first day it became clear that our biggest laser cutting equipment could be out of action for a further 6-12 hours. All of the affected clients were contacted again to update them with the cause of the problem, estimated timescales and the opportunity to cancel their orders should the risk of delays cause them timescale issues.
The next morning two more specialist refrigeration engineers arrived with the parts required to get the equipment running again. It took most of the working day to repair and test the equipment but importantly we were running again. Within a few hours of the machine being repaired we had already produced over a thousand components, and because of amendments to the shift patterns and production schedule we were able to ship out all orders during this period within the agreed timescales leaving no one disappointed.
A long term plan already exists to prevent such issues and during 2015 we are looking to install more laser cutting equipment and automation systems that will bring us into the bulk manufacturing markets. We vow not to become complacent with extra machine capacity and will always be prepared for the unexpected as best as we can.
Such preparedness exists throughout our company from the workshop through to the offices. All of our electrical equipment is not only surge protected but all of our IT equipment and telecoms have uninterruptible power supplies (UPS) to prevent data corruption or equipment loss. In the event of a power outage during unmanned production, the system is able to remain active long enough to send a message to the managers of the company warning them of a problem.
We have backups of our backups backup. As we do not believe that the cloud is a reliable and importantly a secure resource just yet, all of our backups are held in our possession securely on and off site.
If you are a client of ours you can rest assured that we are not only prepared for the worst, but that you will also be kept informed as soon as something unexpected occurs allowing you to make the decisions required regarding your own production and delivery schedules.
If you are not currently a client of ours its worth thinking about your existing supplier, how they would cope during a crisis and how it could impact your business if something were to happen to them from equipment breakdowns to data loss.